Student Placement – Bevaringscenter Fyn
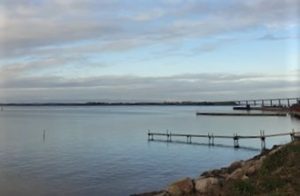
Hi! My name’s Katie, and as part of the second year of the conservation course I’m currently interning at Bevaringscenter Fyn in Denmark. This isn’t exactly how I thought my internship year would go. Denmark’s been in lockdown now for 14 days at the time of writing, meaning that I haven’t been able to gain access to the lab or the objects I’m working on for two weeks. When I was thinking of what to write a blog about, initially I thought that I’d wait until I’d finished working on a pair of 14th century waterlogged leather shoes so I could show how they were conserved from start to finish. However due to a recent turn of events there’s been a bit of a delay in their conservation, meaning that we’ve had to get a bit creative with the methods we’re going to use to ensure their preservation.
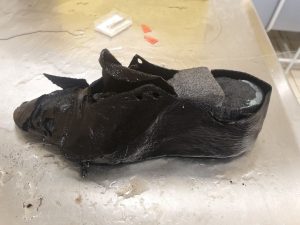
Conserving these shoes has been a real battle. One of them is lovely, well preserved, flexible, mouldable to a last and actually looks like a shoe. The other is a complete nightmare. Very brittle, and refused to be cleaned by cracking and flaking into tiny pieces every time I touched it. On top of all that, the freeze-dryer that we have in the lab here has broken, and due to Covid-19 no one is coming to repair it. So, we’re going old school and making our own non-vacuum freeze-dryer. “What? How?” I hear you ask from across the North Sea. Keep reading, I’ll tell you.
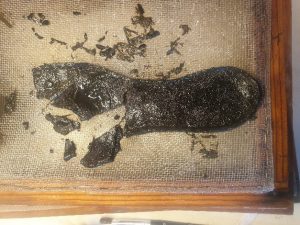
I started working on these shoes back in October, they were one of my very first projects to start on. I’m so interested in waterlogged organics so initially I was so excited to work with them. I started with the first shoe, which was an absolute treat, gently washing it over mesh netting with lukewarm water from a shower head and agitating the dirt with a soft brush. This shoe was very easy to clean as it wasn’t massively degraded. The second shoe couldn’t have been more different. Brittle, easily breakable, awful to work with. Every time I tried to clean it another piece came off and eventually I had to stop cleaning and hope that once it’s dry I can brush more of the dirt off. I organised the pieces that had broken away into logical groupings so that they wouldn’t float away from each other in storage. I put each piece in between breathable polythene sheets, and sealed around each piece using a soldering iron so that the pieces wouldn’t move around while they’re in water or later PEG. While the leather was still wet, I made technical drawings of each piece on a piece of melinex and later transferred the drawings to paper. This is important to do while the leather is closest to its original shape, as the conservation process might shrink the object and we need to record how much by.
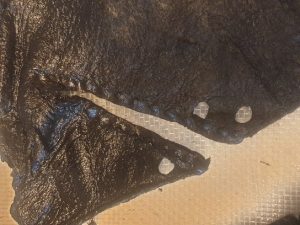
After cleaning, the majority of the hard work was done. The clean pieces of leather were placed in a 10% solution of PEG 400 in water. The leather was stored at room temperature in PEG 400 for about 10 weeks.
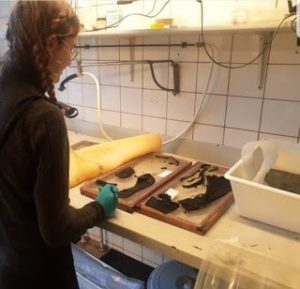
Because the first shoe was so flexible, we decided that it could be moulded round a last into a 3D object. A last is a mould that cobblers use to make it easier to put all the elements of the shoe together. In medieval times they were made from wood to suit the person that the shoe was being made for. In conservation they’re useful because the leather can be pinned to the last which we make from ethafoam, and the leather dries into the shape of the mould. It’s much easier than drying the leather flat and then trying to shape it afterwards. So I made the last, it took about 5 tries to get the shape right, and pinned the pieces of leather through the existing stitch holes to the ethafoam so it can dry in a shoe shape. The leather is currently in the freezer waiting to be dried.
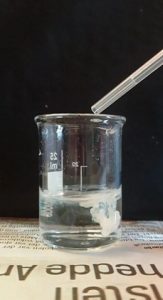
Unfortunately, we discovered that the computer controlling the freeze dryer is no longer working. Due to Covid-19, no one is available to fix or replace the computer. It means that we can’t dry the shoe using the conventional method of controlled vacuum freeze-drying, so we’re getting creative. We can’t air dry the leather as it risks drying the object too quickly which will result in shrinkage and cracking. We were having a look through the literature when we stumbled across an email from 1998 describing a way to make your own non-vacuum freeze dryer. It’s not ideal, because it’s less controllable than the vacuum freeze dryer, but with no one available to fix our computer until probably June it’s worth a shot.
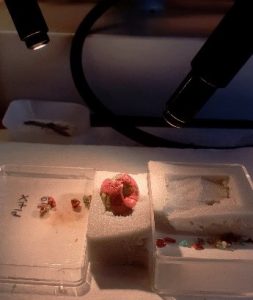
To make a non-vacuum freeze dryer, we’re going to need a freezer, a fan and silica gel. The leather will be placed on a thin layer of plastazote on top of open mesh baskets. The baskets will be put between the fan and the silica gel to allow a flow of cold air over the leather towards the silica gel. The silica gel will reduce the humidity of the freezer, and the leather will slowly dry out. This method is fairly easy to carry out, but will take longer than the conventional method. However in the current situation it’s probably the best we can do, and hopefully the leather will come out the other side in good condition.
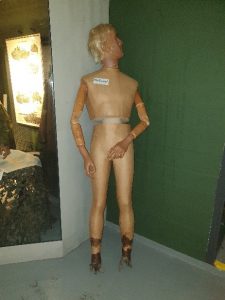
Once the leather is dry, it will need consolidating. The drying process may make the leather flaky and it might start delaminating. So I’m planning to use a 2% solution of Klucel G in ethanol to consolidate the shoes, it will have to be used over the entire surface of the leather as the solution will darken the leather. Pieces which need adhering can be done so with a higher solution of Klucel G in ethanol, or Lascaux 498 HV in isopropyl alcohol. Lascaux 498 dries clear and provides a strong bond with repair tissue that helps retain flexibility. The second shoe which has broken into lots of pieces will be attached to a backing, which will provide it with some more strength and then may be able to be moulded around a last but the most important thing is that the pieces stay together.
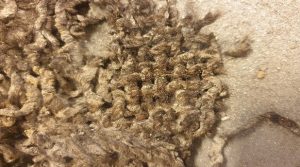
The shoes have been an exciting and frustrating part of my time here, and I’m excited to see how this home-made freeze dryer works once I’m allowed back in the lab. I have a range of things to be working on which is really exciting. On top of the waterlogged leather I’ve been working on a very large group of iron age amber beads, a clay firedog (a stand for pans on a fire), an environmental report for the local museum, the rehousing of an archaeological textile and examining the reliability of methods used for chloride testing. As well as the projects I’ve been able to take part in things such as helping with a condition survey of a museum collection, where we had to board a ferry to get to the museum (!), and rescuing objects from another museum after disaster struck and a pipe burst. The experience here is amazing, and it’s really interesting to see how different one day can be from the next. The unpredictability of the job is probably one of my favourite things.
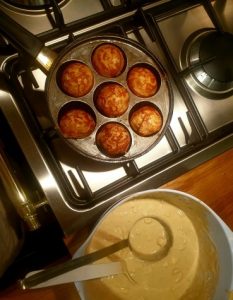
I’ve been in Denmark for 5 months now, and it’s been an invaluable experience to work here. Not only do I have some really cool projects to work on, I’ve been participating in lots of social events too. I have felt so welcomed by everyone, invited to go to the Julemarked (Christmas Markets), made æbleskiver – kind of like donuts but better – had a day trip to Copenhagen for a vegan festival. It’s really true to say that the people do make the place, and I feel so lucky to have met the people I have. So even with everything going on right now and my projects come to a bit of a standstill, I’m really enjoying being out here and just can’t wait to be back in the lab!
Katie